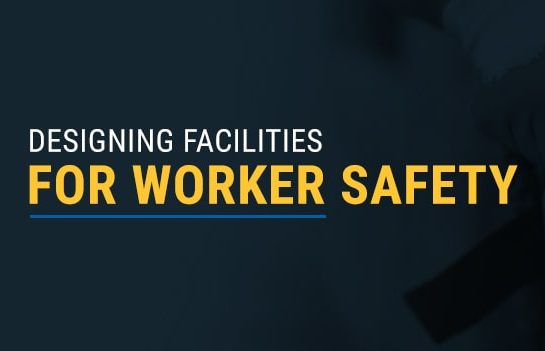
Designing Facilities for Worker Safety
June 16, 2021
Worker safety is paramount to a facility’s success, and it all starts with design. If you can eliminate a hazard at the source, you reduce the need for protective measures and the overall risk. So what goes into cultivating workplace safety, and how do you focus on your facility’s unique needs? Let’s take a closer look at safe facility management and the design of a workspace that supports occupational safety.
Facility Hazard Analysis
The first step to creating a safe workspace is to assess it. We can break down a facility analysis into a few different sections:
- Structures: Consider the characteristics of the structures you’ll be working on and around and what you can logistically use with them. For instance, anchoring mechanisms will vary between safety devices. If using a fall arrest system, you’ll need to make sure it will work with the structure presented. Working with very large items, such as aerospace equipment, will call for specialized mechanisms to safely get workers to the right heights.
- User needs: Do your workers need fall protection, head protection, respiratory protection, or something else? The different types of hazards that could exist on a work site need to be identified before you can address them. Then, identify what is needed for protection, including respirators, hard hats, cut-resistant gloves, work boots, fall arrest systems, and more.
- Unique elements: Consider any specific hazards that might be present due to unique factors in the location. Are there low-hanging power lines that would prevent aerial work outdoors? Is there some kind of structure that could interfere with the fall protection system? Does your facility have hazards like fire, fast-moving machinery, or corrosive chemicals that could be a danger to workers?
- Response requirements: In the event of an incident, what is needed to respond to the problem? You’ll need to have plans in place and equipment nearby. Will you need eye-washing stations in the event of chemical exposure? How about first-aid kits within reach of different parts of the facility and a plan to rescue workers after a fall arrest system has been used? Consider the response needed in all of the hazards you’ve identified.
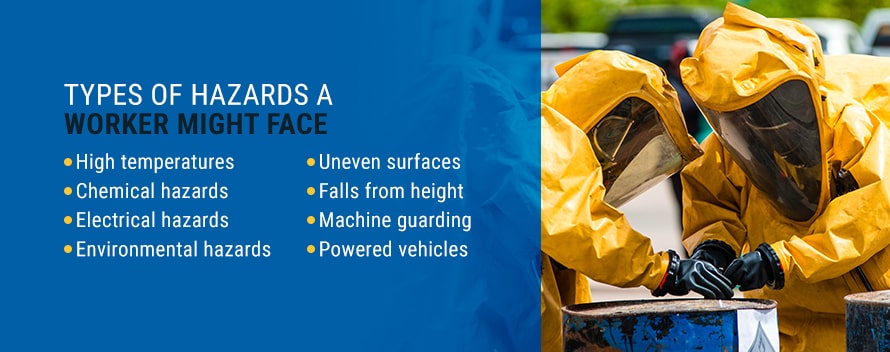
Types of Hazards a Worker Might Face
There’s no shortage of hazards in an industrial workspace. In 2018, the top causes of work injuries that were treated in an emergency department were workers having contact with equipment and objects, overexertion or bodily reaction, and falls, trips, and slips without a fall. Identifying and preventing these and other workplace hazards is a critical part of work site safety.
Consider the following hazards that could occur on the work site:
- High temperatures: Many industrial processes call for high heat. From superficial burns to more permanent damage, high heat is a clear danger. Workers need to be well-trained on processes involving high heat and protected from machinery while it’s running.
- Chemical hazards: Chemicals are often a big part of daily operations for industrial facilities and can lead to burns, respiratory problems, and long-term illness. Proper training, equipment, and response tools are necessary for working with chemicals.
- Electrical hazards: Even if employees aren’t working directly with electrical components, there are many electrically powered machines that could pose a threat. A loose wire or detached panel could quickly cause trouble and lead to electric shocks or arc flashes.
- Environmental hazards: A facility environment can be filled with all sorts of threats, like combustion gases from work processes and tobacco smoke from an employee smoking near the door. In older buildings and some processes, workers could be exposed to materials like lead and asbestos or dangerous pesticides.
- Uneven surfaces: Uneven surfaces, such as a cracked floor or a piece of duct tape peeling up from the floor, can create a trip hazard. For employees working at heights, uneven surfaces could cause a more serious fall risk.
- Falls from height: Working at heights often requires strong safety precautions, such as fall arrest systems and buddy system policies, to mitigate the serious risk of a fall and the complications that come with it, including suspension trauma. It’s also important to minimize hazards on the ground, such as spills, loose material, and trip hazards.
- Machine guarding: Heavy equipment can move quickly, with sharp objects or heavy forces involved. Keeping workers safe from these dangerous components requires machine guards and safe work practices like wearing the right personal protective equipment (PPE), keeping long hair pulled back, and other best practices.
- Powered vehicles: Industrial powered vehicles are a significant cause for concern in the workplace. While proper training is essential, you can also adjust the layout of the workplace to make forklift driving safer. Placing mirrors around sharp corners to eliminate blind spots and ensuring a well-lit environment are a few ways to reduce problems.
Questions to Consider
When designing a facility with worker fall protection safety in mind, consider the following questions.
1. Is There Enough Space for Fall Protection Equipment?
If fall protection is needed, you will have to ensure there’s enough room for it. There are many different configurations available for rigid rail fall protection systems, so it’s likely there’s a suitable option for your setup. Use your analysis of the location to see how much room you have and compare that with the equipment you’re looking at.
2. Is There Enough Space for Post-Fall Rescue?
Post-fall rescue is an often overlooked aspect of fall protection. You’ll need to account for your post-fall rescue plan when determining a facility layout to minimize the risk of suspension trauma to a fallen worker. These methods can vary widely, and we’ve written some blog posts on the subject if you want to learn more about post-fall rescue mechanisms. What’s important for your facility design is that you leave room for these tools, such as ladders, lifelines, trauma relief packs, and controlled-descent devices.
3. What Equipment Will Workers Be Working Around?
When determining the layout of the facility, consider how nearby equipment could affect workers. In the event of a fall, does the equipment pose a greater threat, such as placing a worker near a chemical hazard while suspended? Does work on certain pieces of equipment call for greater fall protection? Carefully assess all equipment to identify how it could be a hazard during typical work and during a fall.
4. Is There Anything That Can Be Done in Layout Planning to Eliminate Hazards?
Designing a facility layout offers countless opportunities to reduce or eliminate hazards. There are many simple things you can do, like placing safety mirrors on forklift paths or moving a piece of machinery to keep its hazards away from areas with heavy traffic. You can also add specially configured fall safety equipment to prevent hazards in a way that’s well-suited to your unique facility environment.
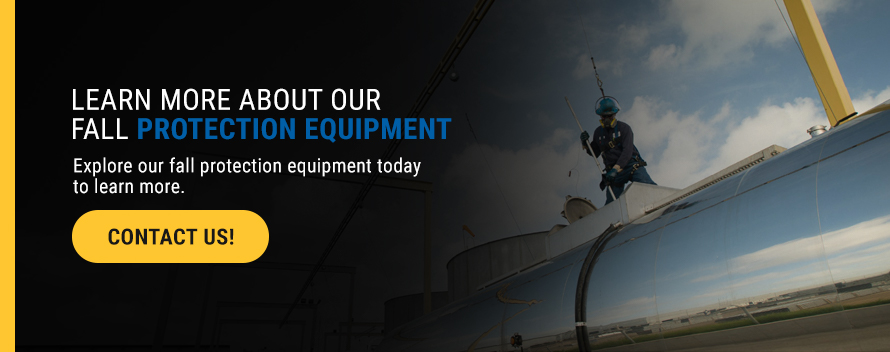
Learn More About Our Fall Protection Equipment
The experts at Rigid Lifelines have been engineering, designing, and testing fall protection systems for over 20 years. Whatever your facility layout looks like, we can help you find the right rigid rail fall protection system that meets Occupational Safety and Health Administration (OSHA) and American National Standards Institute (ANSI) standards and regulations to protect workers from hazards and create a safer, more reliable workspace.
Explore our fall protection equipment today to learn more.
Categories
Share this post
Let us help you
Contact us today to find the perfect product fit for your job
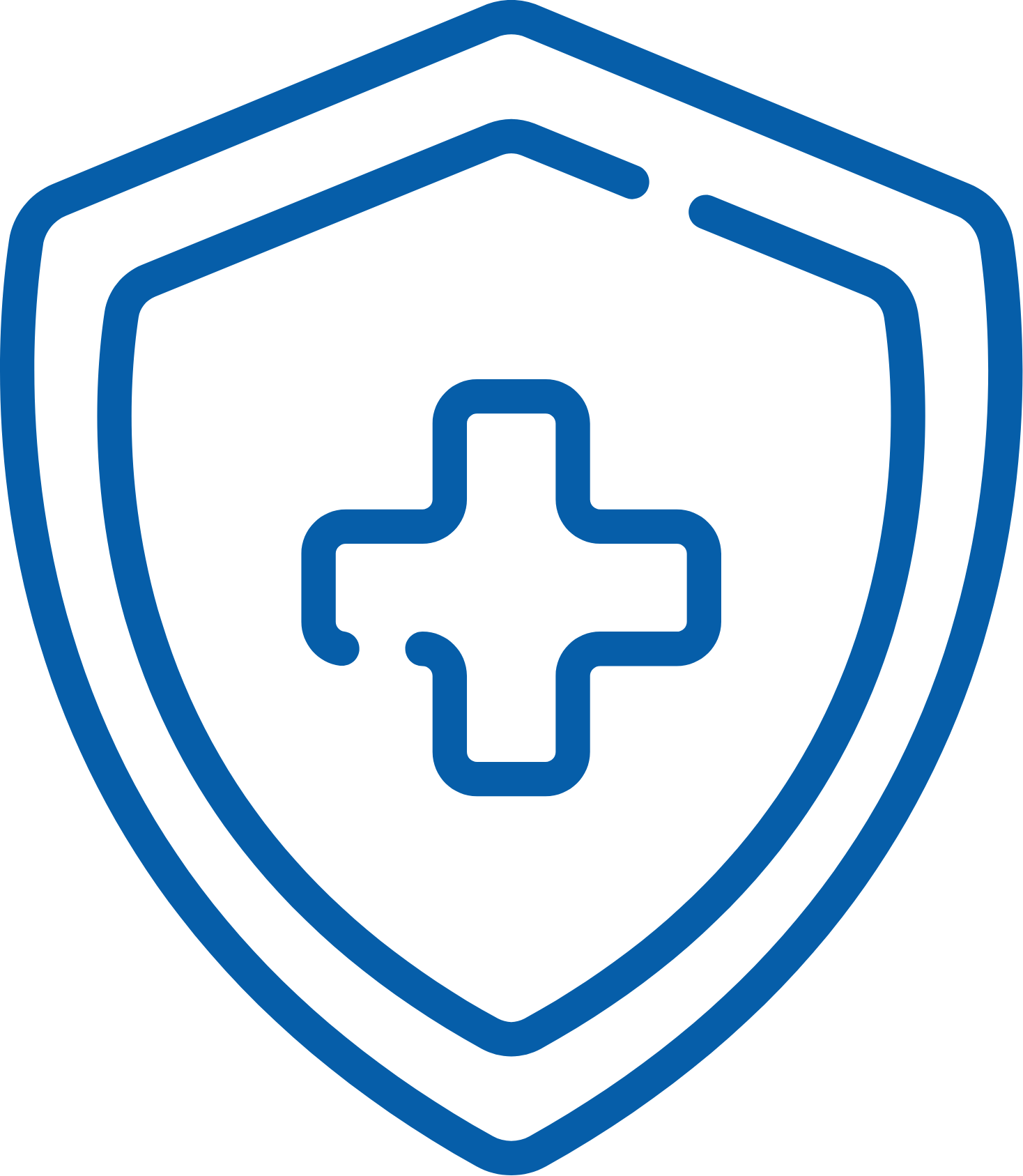