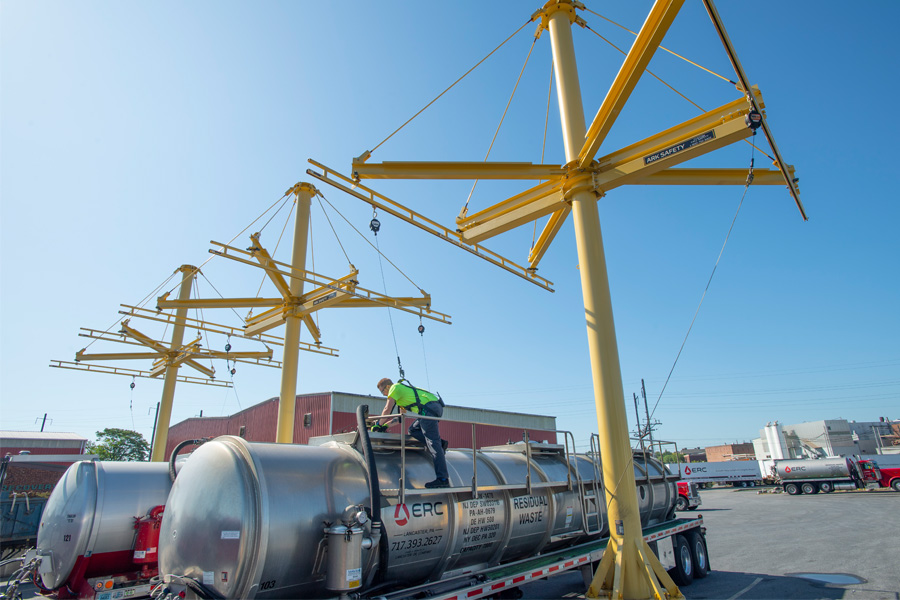
A Brief History of Fall Protection
September 17, 2024
Before the Occupational Health and Safety Act (OSHA) of 1970, fall protection in the workplace was not regulated in the United States, and employers bore little responsibility for fall hazards. Let’s walk through the history of U.S. fall protection standards, starting with early workplace safety.
Early Workplace Safety
In the early days of industrialization, workplace safety was often neglected, leading to numerous hazardous conditions. Machines were frequently unguarded, so workers were at constant risk of injury from moving parts, shard edges, and mechanical failures. Power sources such as steam engines and early electrical systems were often poorly maintained and lacked proper safety measures, increasing the risk of explosions, fires, and electrocution.
The lack of interest in improving safety stemmed from a combination of factors. Employers were primarily focused on maximizing productivity and minimizing costs, often at the expense of worker welfare. Additionally, there was limited regulatory oversight and few established safety standards, so the incentive to invest in safety improvements was minimal.
Many injuries and deaths occurred during this time due to working at heights with zero fall protection equipment and multiple other work hazards. Each worker was supposedly responsible for his or her own safety, and workers believed safety devices to be too restrictive and cumbersome to be of value.
Substantial improvements in the workplace began only after the rise of labor movements and the implementation of safety regulations in the late 19th and early 20th centuries.
Fall Protection Evolves
With the advent of OSHA and with the increasing costs of litigation related to deaths and injuries from falls, attitudes about workplace safety began to change. Fall protection became a more significant priority.
Industries such as construction, manufacturing, mining, and transportation began to see the value in providing passive — ladders and enclosed walkways — and active — rope and body belt systems — fall protection for workers. Massachusetts was the first U.S. state to implement safety and health legislation in 1877.
The risk of OSHA spot inspections and heavy fines for noncompliance with regulations added a new incentive for employers to address potential fall hazards in the workplace.
On the technological side, you can trace most active fall protection systems to mountaineering, where the need for fall protection is obvious. Mountaineers and rock climbers have long used complex fall protection systems that include some of the same elements seen in industrial fall protection, including anchorage devices, ropes and lanyards, and body harnesses.
Safety Body Belts
During the 1970s and 1980s, safety body belts became the norm for workers who needed to do specific tasks high up. Body belts were inspired by rock climbing equipment. The construction industry added the protection of the “100% tie-off,” which required that two lanyards secure a worker’s body belt. This ensured that at least one lanyard would remain attached, even at transition points between work areas. Workers, however, found the tying and untying of lines time-consuming.
Full Body Harnesses and D-Rings
By the 1990s, the full-body harness began to exert itself in the workplace. For the first time, workers had protection at height not only from fall-related impacts but from the spinal and internal organ injuries that could result from even short periods of suspension from a body belt. The dorsal D-ring, an essential piece of any harness, provided a more effective weight distribution. D-rings are tie-down rings acting as anchors placed on the center of the back.
Advances in the materials used in the construction of harnesses made them more comfortable, able to hold heavier workers, and more resistant to wear and tear from weather and exposure to corrosives and abrasives. The development of the self-retracting lanyard helped reduce fall distance, improve deceleration, reduce sudden stops, and improve ease of rescue.
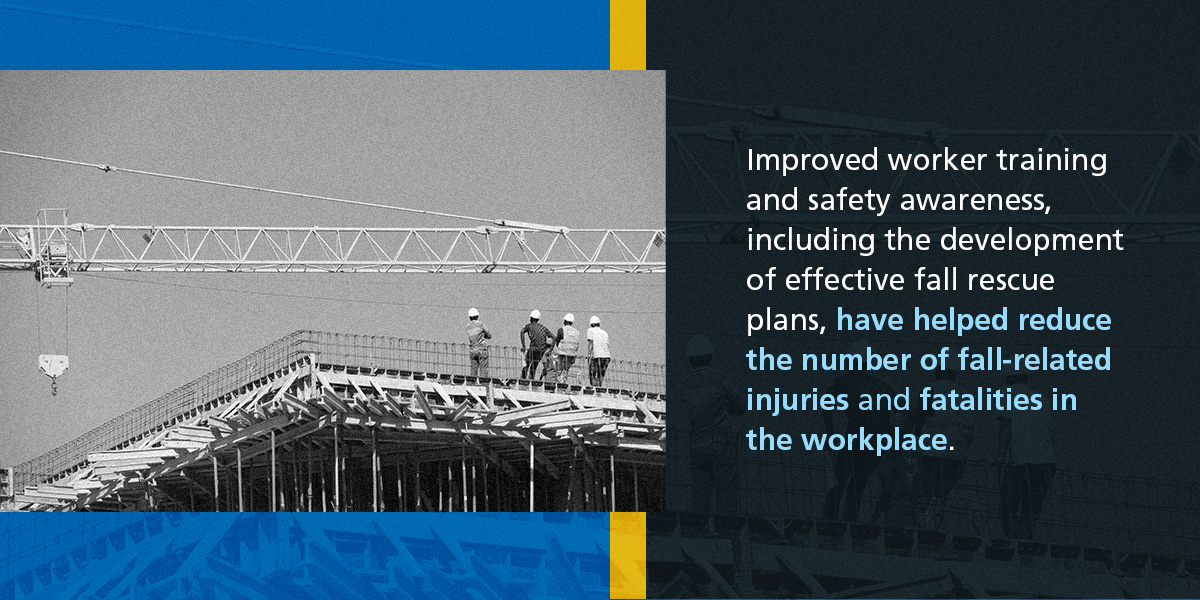
Improved worker training and safety awareness, including the development of effective fall rescue plans, have helped reduce the number of fall-related injuries and fatalities in the workplace.
History of Fall Protection for Residential Home Construction
A 2011 change to OSHA’s 1999 fall protection standards expanded the agency’s regulatory scope to require fall protection for residential home construction.
According to the new regulations, personal fall arrest systems must:
- Not allow workers to fall over 6 feet or to contact a lower level
- Bring a worker to a complete halt with a maximum deceleration distance of 3.5 feet
- Have the strength to hold two times the impact energy of a free-falling worker with a distance of 6 feet — or the fall distance permitted by the system, whichever is less
Choose Your Fall Protection System With Rigid Lifelines
The history of fall protection includes tremendous advances in worker safety practices. Fall protection continues to evolve, and manufacturers and safety professionals are seeking new and innovative ways to identify hazards and protect workers.
Rigid Lifelines® provides various fall protection systems to keep workers safe at height. Contact us to help you choose the fall protection system that best meets the needs of your business, your facility, and your workers.
Categories
Share this post
Let us help you
Contact us today to find the perfect product fit for your job
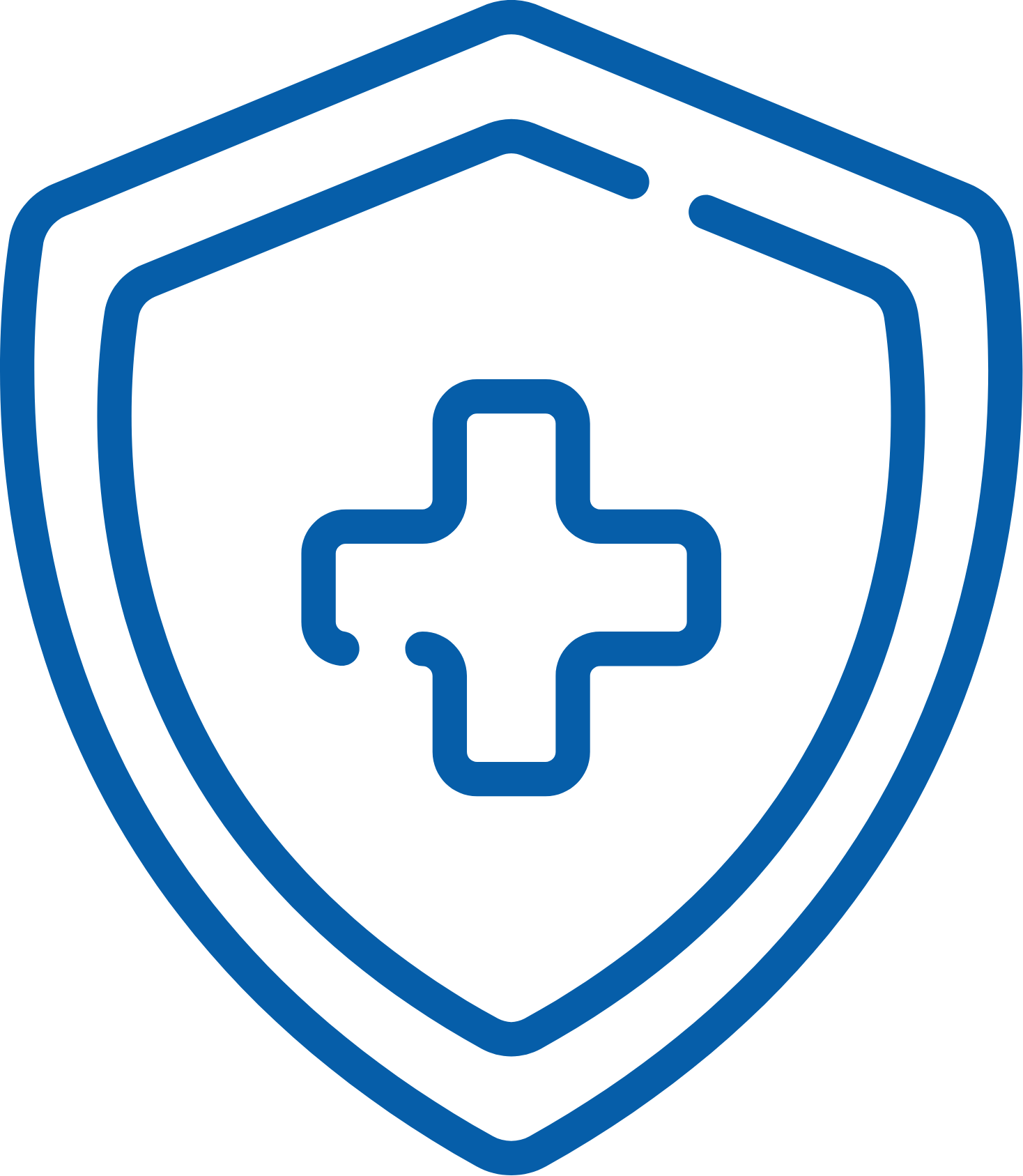